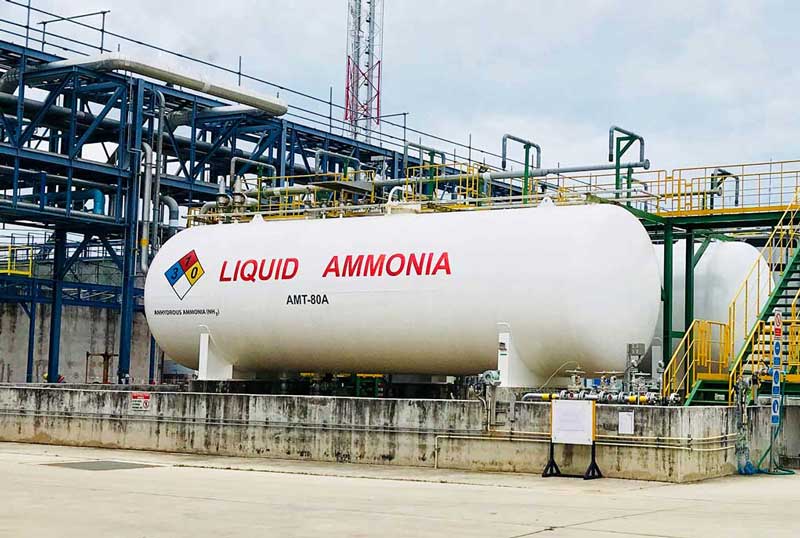
Ammonia (NH3) is produced by the catalytic reaction of nitrogen and hydrogen. It can also be found naturally, from the decomposition of plants, animals and animal waste.
- About 80% of the ammonia produced by industry is used in agriculture as fertilizer.
- Ammonia is also used in the manufacture of plastics, explosives, textiles, pesticides, dyes and other chemicals.
- Ammonia plays an important role in the energy transition because it is a flexible, long-term energy carrier and zero-carbon fuel.
What is Green Ammonia?
Ammonia can be made synthetically by combining nitrogen with hydrogen, in a process called ammonia synthesis. When this process is completed using renewable energy sources with zero carbon emissions (such as wind, solar, hydropower and geothermal energy) the result is green ammonia. Ammonia synthesis is achieved by combining green hydrogen and nitrogen at high temperature and pressures (modified Haber-Bosch Process):
Green Ammonia is often used as a:
- Hydrogen carrier over long distances
- Fuel for engines, such as locomotives and ships, replacing diesel and marine fuel oil
- Fuel for electricity power generation
- Building block to make fertilizers, and a feedstock for industrial applications.
What is Blue Ammonia?
Blue ammonia is made from nitrogen and hydrogen derived from natural gas feedstocks, with the carbon dioxide by-product from hydrogen production captured, utilized or stored (CCUS). The product characteristics of blue ammonia are identical to conventionally produced ammonia.
Blue Ammonia is manufactured by converting gaseous nitrogen (N2) and hydrogen (H2) in synthesis gas (Syngas) in the presence of a catalyst. The Syngas comes from Hydrogen, which is produced by reforming or gasification of fossil feedstocks combined with CO2 Capture.
Today, there are three primary methods for producing Blue-H2
- Steam Methane Reforming (SMR): is the most widely deployed technology. SMR involves reacting natural gas with steam in the presence of a catalyst at high temperature to produce hydrogen. Approximately two-thirds of the CO22 is in concentrated form during hydrogen production. The remaining third is generated in dilute form in the flue gas from burning natural gas for heating purposes. Post-combustion carbon capture can be retrofitted to convert grey hydrogen production to blue.
- Autothermal Reforming (ATR): improves the cost-effectiveness of SMR by adding Oxygen to the process and a higher overall energy efficiency. In ATR, pure oxygen is supplied for combustion which results in a concentrated and high-pressure stream of CO2 making carbon capture integration easier. This requires a substantial feed gas pretreatment investment and the fired heater produces CO2 emissions.
- Partial Oxydation (POX): reactions between oxygen and hydrocarbons in the reformer produce H2 rich syngas. It is a noncatalytic process that does not consume steam and has no direct CO2 emissions. With no need for feed gas pretreatment, POX technology is simpler than ATR.
Blue syngas is further processed to adjust the gas mixture composition. It is then purified in a CO2 removal section to produce blue hydrogen-rich syngas, and it also goes through a methanator unit which removes the remaining CO and CO2. Finally, Blue ammonia synthesis is achieved by combining and reacting blue H2 rich syngas and nitrogen at high temperature and pressure (modified Haber-Bosch Process).
Blue ammonia is a high-volume carrier of hydrogen energy. It helps hard-to-abate industries (such as transportation and power generation) decrease their carbon intensity.
Pump Applications for Ammonia Production:
Some ammonia solutions (at concentrations of 25% or higher) are corrosive, so the pumps used to produce ammonia must be durable and reliable. A wide range of pumps are used in Green and Blue Ammonia Production, including:
Pump Applications:
- Boiler Feed Water Circulation Pumps
- Hydrogen Condensate Pumps
- Sea Water Pumps
- Cooling Water Pumps
- Corrosion Inhibitor Pumps
- Water Feed & circulation Pumps
- KO Drum Pumps
- Amine Circulation & Booster Pumps
- Wash Water Pumps.
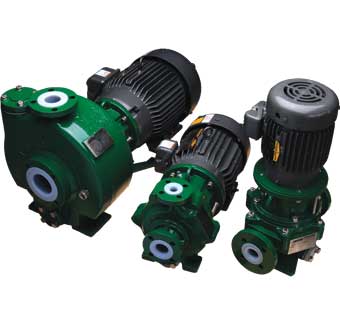
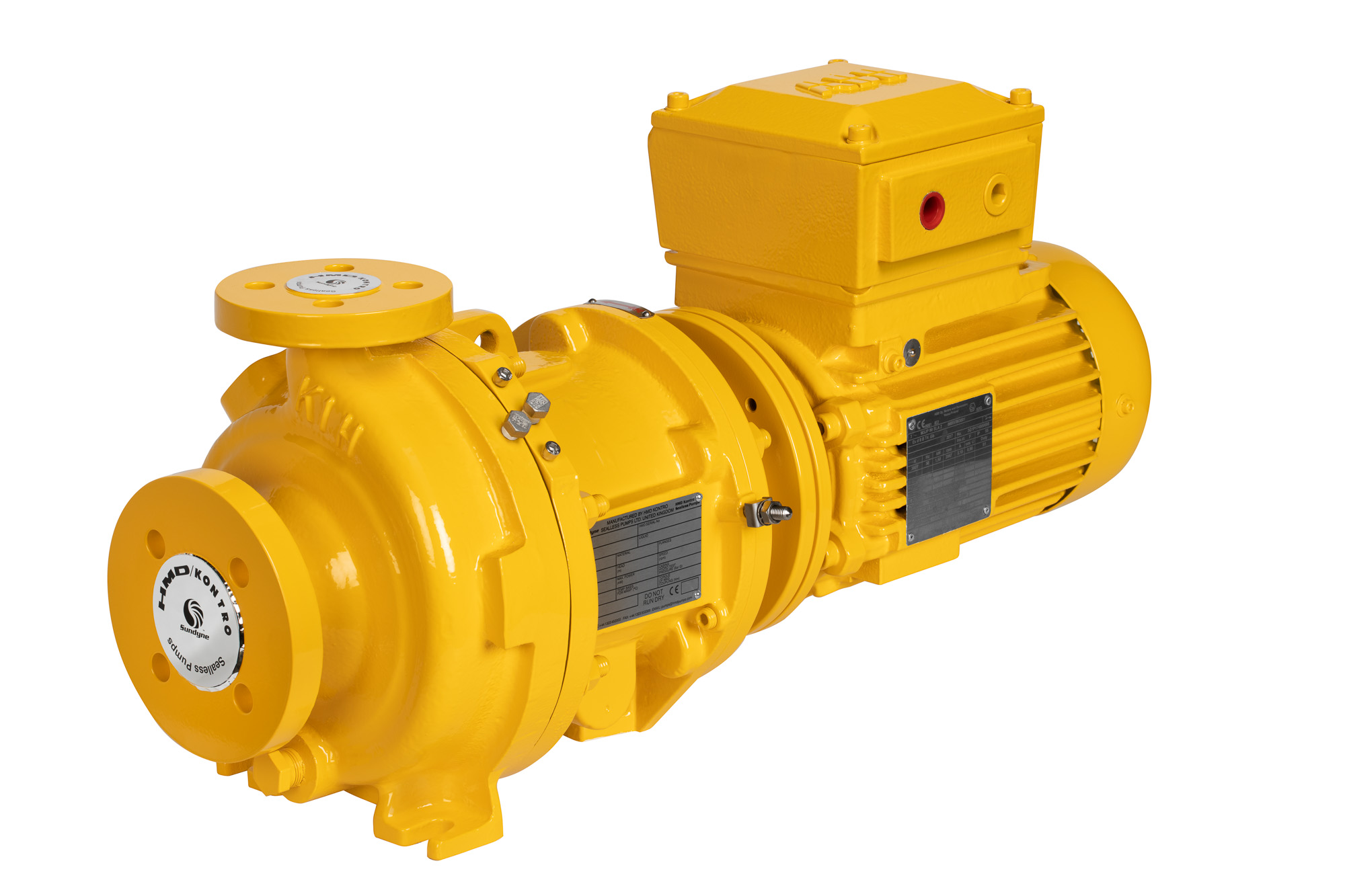
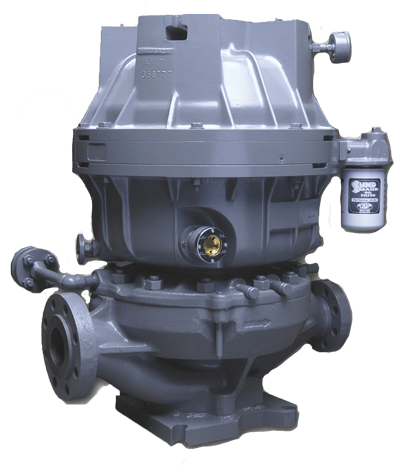
Operators should consider the following criteria when selecting pumps for ammonia applications:
- Reliability: ammonia plants are built to run for 20-50 years. Sundyne equipment has a service life of 30 years and some units have operated for more than 50 years.
- Efficiency: the footprint of Sundyne equipment allows users to install additional equipment in less space, like the addition of CO2 capture on existing plants. Sundyne’s 70-plus year track record makes it easy for operators to run equipment at Best Efficiency Point (B.E.P.)
- Worker Safety: Ammonia pumps are subject to strict safety regulations. Sundyne liquid mechanical seals and dry-gas seals are proven for use in the petroleum, chemical and gas industry services. Ansimag and HMD sealless pumps are leak-proof by design, with fully enclosed wet-ends that eliminate leakage.
- Superior Chemical Resistance: Ammonia processing can wreak havoc on rotating equipment’s internals. A wide range of metallic and ETFE materials are available to address any process requirement.
- Simplified Maintenance: The global volume of ammonia production illustrates the need for reliable equipment that minimizes plant downtime. Sealless pumps have fewer parts and no seal support systems, which increases Mean Time Between Maintenance (MTBM), and minimizes costs.
For decades, Sundyne has worked with the world’s largest ammonia producers, pioneering many of the technologies that are commonplace today. To learn more about pumps for Ammonia production, please visit sundyne.com/industries/ammonia.