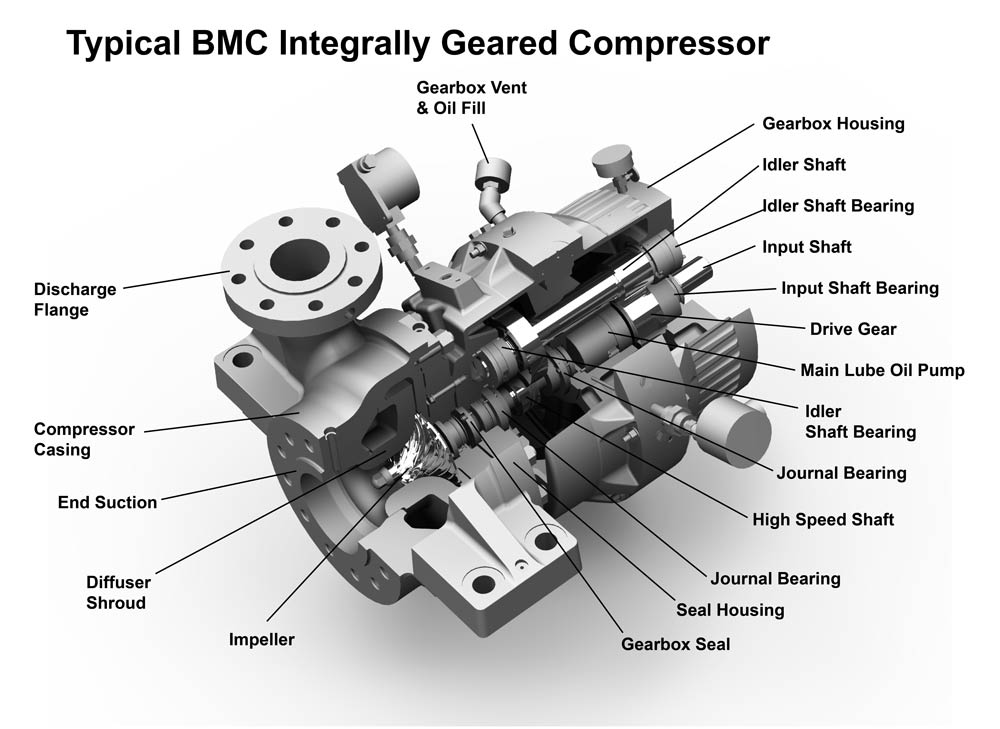
What is a Centrifugal Compressor used for?
Centrifugal compressors move gas from point A to point B. They’re also used to increase gas pressures. A good example comes from the power generation industry. In power plants, gas turbines require gas inputs to be approximately 250-750 psig – but interstate pipelines move gas at pressures of just 30-125 psig. In order to run turbines in an optimal fashion, the pressure of the gas inputs must be boosted – and centrifugal compressors are used to do this.
How do Centrifugal Gas Compressors work?
Centrifugal compressors elevate gas pressure by adding kinetic energy/velocity to the gas as it flows through an impeller. Kinetic energy increases potential energy/static pressure by slowing the flow through a diffuser. The pressure rise in the impeller (in most cases) is equal to the rise in the diffuser.
As the flow passes through the centrifugal impeller, the impeller forces the flow to spin faster as it gets further from the rotational axis. The energy input applied to the gas flow is proportional to the flow’s local spinning velocity multiplied by the local impeller tangential velocity. The flow leaving the centrifugal impeller travels at an accelerated rate, until it flows through a stationary compressor, which causes it to decelerate, and energy transformation takes place. The reduction in velocity causes the pressure to rise.
What is the difference between a Centrifugal Compressor and a pump?
Centrifugal compressors move gas, and centrifugal pumps move liquid.
What is the difference between a Reciprocating and Centrifugal compressor?
A Reciprocating compressor is designed somewhat like an internal combustion engine, in that it utilizes pistons that sit inside cylinders to compress air/gas. For compression, the pistons draw back as gas is injected from intake valves in the compressor. After the gas is injected into the cylinders, it’s compressed by the reciprocating motion of the pistons. The differences between Centrifugal and Reciprocating compressors are as follows
- Centrifugal compressors have better isothermal efficiency, and they score higher on isentropic efficiency. Centrifugal compressors don’t require as much maintenance as reciprocating compressors. (Reciprocating compressors can have a multistage operation. While this is advantageous for some applications, multistage systems require more maintenance than their single-stage centrifugal counterparts.)
- Reciprocating compressors are more flexible than Centrifugal compressors, and they work well with changing pressures. Centrifugal compressors are better for low pressure and high discharge operations because they work at a constant rate.
What are the main parts in a Centrifugal Compressor?
The main parts in a centrifugal compressor include the: impeller, gearbox, idler shaft, input shaft bearing, drive gear, seal housing, gearbox seal, diffuser shroud, discharge flange, and the compressor’s casing.
For more information on Sundyne compressors, click here.