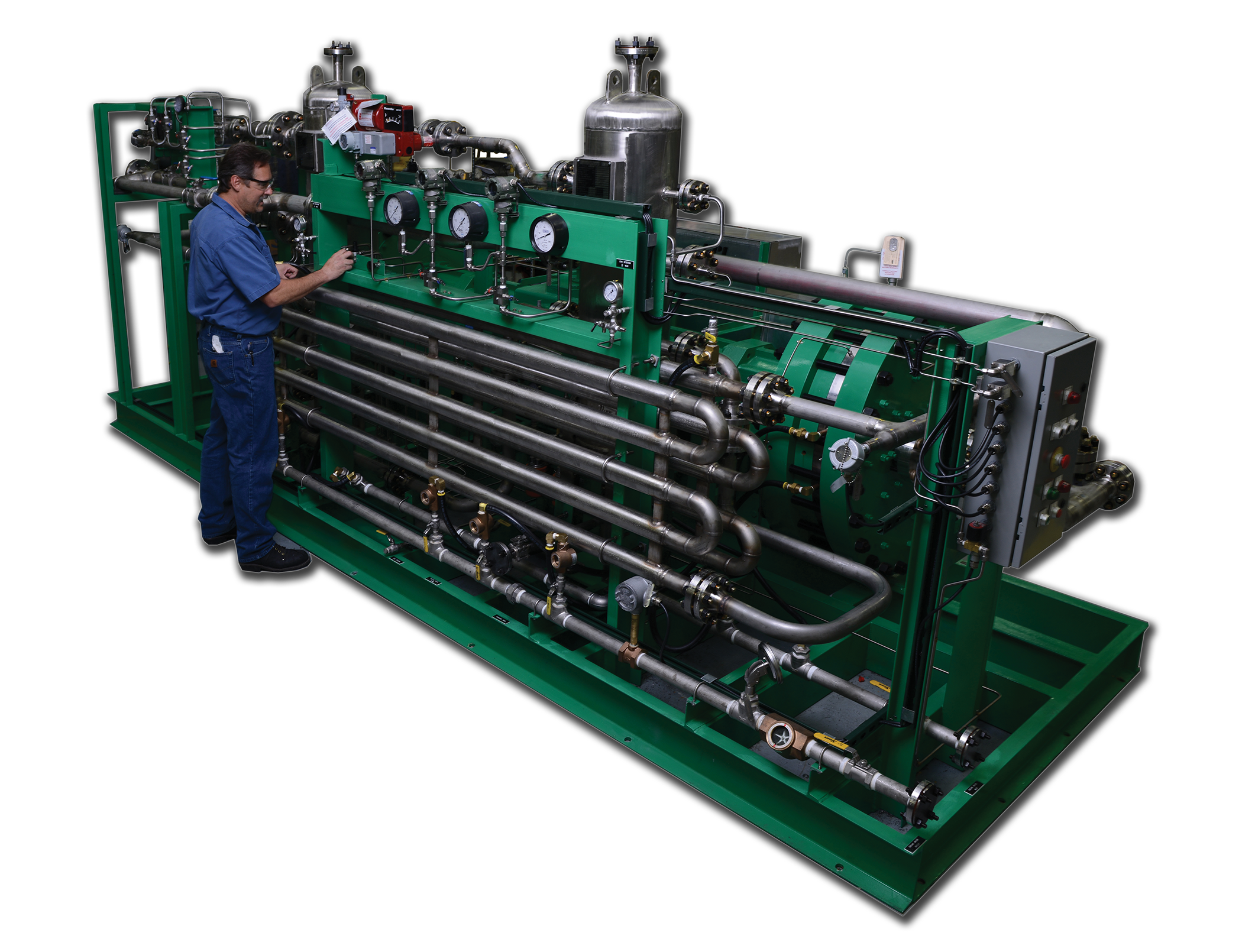
Designed for processes engineers requiring reliable operation in the full range of high pressure services
The Series 9X Diaphragm Compressor is for pressures up to 5,000 psig and available in single and two stage configurations. Sub-series models are as follows:
- 9X Single Stage
- 9X/H Two Stage
MARKETS
- Petrochemical
- Specialty Gas
- Energy
- Silicon Manufacturing
PPI Diaphragm Compressors Series
All PPI diaphragm compressors deliver total assurance of non-contaminating gas compression. Boasting a leak tight mechanism that features static seals which do not need to be purged or vented, these compressors present absolutely zero leakage threat to the atmosphere, providing an ideal solution for safely handling ultra-pure, corrosive and volatile gases. Additionally, our diaphragm compressors are designed to isolate the process media from the piston or piston rings with a set of metallic diaphragms, completely eliminating the risk of cross contamination. Most models are built to meet API 618 standards where applicable to diaphragm compressors. These machines are available in a variety of flexible configurations and sizes, making them easily customizable to provide the ideal compressor for your application. Backed by our global network of Authorized Service Centers and support staff, PPI sealless diaphragm compressors are the reliability-focused solution for customers operating in the petrochemical, refining, electronic gas, specialty gas and polysilicon production industries.
Durability
We have thousands of compressors installed in extreme operating environments, such as refineries, petrochemical facilities and immaculately clean research centers; but no matter where they are installed, diaphragm compressors deliver high performance, lubricant- and particulate-free compres- sion of gases and mixtures. Plus, our proprietary Ultrafram diaphragm technology and proprietary cavity design provide unmatched diaphragm life.
Reliability
PPI diaphragm compressors feature heavy duty components custom engineered to ensure reliable operation. We performance test every compressor in the factory and document operating data to meet your specific service and operating parameters.
- Proprietary designs evolved from years of field experience assures reliability in the most demanding applications and environments
- Thorough factory testing prior to shipment verifies guaranteed test point
- Critical components, including the crankcase assembly and connecting rod(s), are designed for long life with minimal maintenance
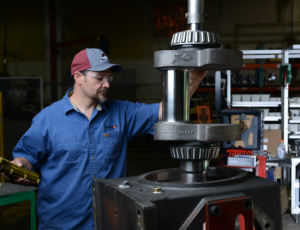
US 60 Hz
- Maximum Working Pressure 5,000 psi
- Maximum Motor Size 250 HP
- Mounting H Configuration
- Maximum Displacement 146.6 ft3/min
- Speed Range 250 to 335 rpm
- Maximum Discharge Temperature 450°F
- Stroke Length 8 in
- Process Connection Flanges 1 to 2.5 in
- Piston Range 3.3 to 11 in
- Crankshaft Diameter 5.5 in
- Crankpin Diameter 4.25 in
- Main Bearing Type Tapered Roller
- Crankpin Bearing Type Babbit Sleeve
- Wrist Pin Bearing Type Roller
- Lubricant-ISO 150
- Lubrication Type Pressurized
- Sump Capacity 34 Qts
- Oil Cooler Required
- Cooling Type Water Cooled
Metric 50 Hz
- Maximum Working Pressure 345 bar
- Maximum Motor Size 185 kW
- Mounting H Configuration
- Maximum Displacement 146.6 ft3/min
- Speed Range 250 to 335 rpm
- Maximum Discharge Temperature 250°C
- Stroke Length 203 mm
- Process Connection Flanges 63 mm
- Piston Range 279 mm
- Crankshaft Diameter 139 mm
- Crankpin Diameter 108 mm
- Main Bearing Type Tapered Roller
- Crankpin Bearing Type Babbit Sleeve
- Wrist Pin Bearing Type Roller
- Lubricant-ISO 150
- Lubrication Type Pressurized
- Sump Capacity 32 Ltrs
- Oil Cooler Required
- Cooling Type Water Cooled
Process Side: Stainless Steel
Crankcase: Ductile Iron
Connecting Rod: High Strength Ductile
Crosshead: Ductile Iron
Cylinder: Ductile Iron
Wrist Pin: Tool Steel
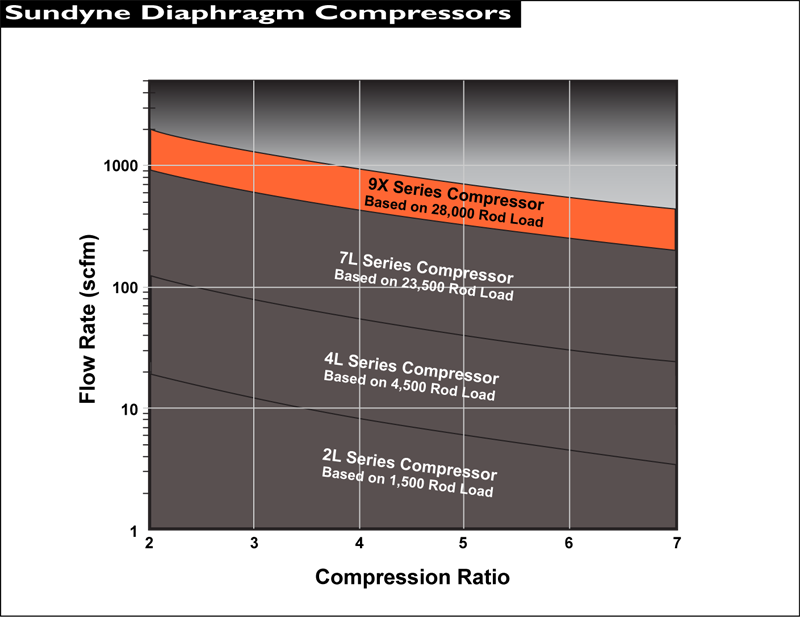