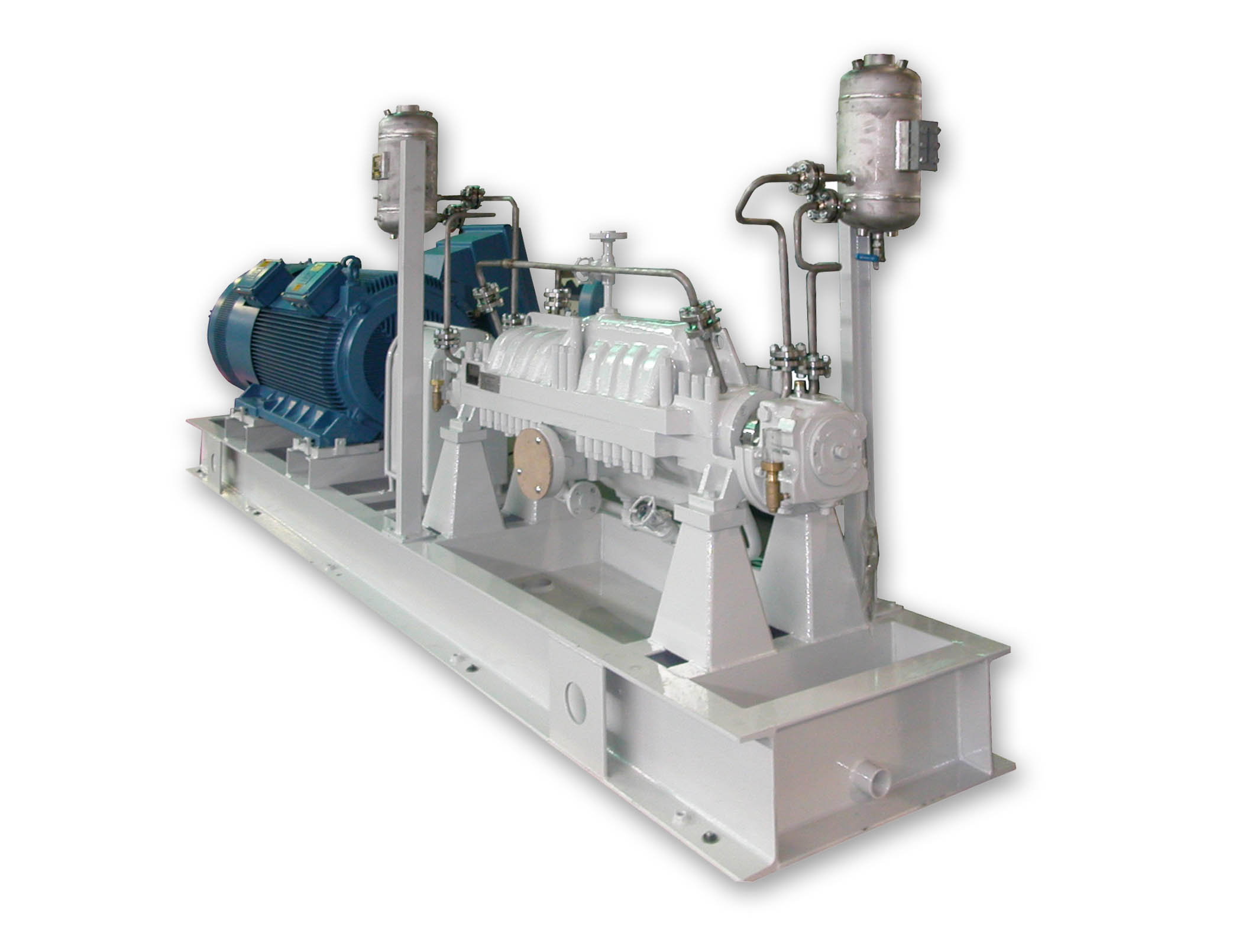
Designed for processes engineers requiring reliable operation in the full range of high pressure services
The DVMX fully compliant API-610 11th Edition BB3 and ISO 13709 multi-stage process pump. Available in 4 – 14 stages. Horizontal axial split case running back to back impellers in heavy-duty double volute casings.
- Flows to 2,640 gpm (600 m³/hr)
- Heads to 4,260 ft (1,300 m)
- Suction Pressure 232 psi (16 bar)
- Temperature Range -40 to 410°F (-40 to 210°C)
Precision engineered API/ISO 13709 process pumps meeting rigorous engineering requirements for heavy duty, high temperature applications while receding the total life cycle cost and improving mean time between repairs. A perfect high-flow, high-head compliment to Sundyne low-flow, high-head integrally geared LMV and BMP centrifugal pumps.
APPLICATIONS
- Boiler feed water
- High pressure water services
- Crude oil pipeline
- Crude products pipeline
- Water injection
- High pressure condensate
- Propane transfer
- Gasoline pipeline service
- NGL pipeline
- Mine dewatering
- Water flood
- HP amine circulation
- High pressure refinery services
- Process charge
- De-scaling
- CO2 injection
Proven to be reliable, efficient and long-lasting, Marelli BB3 pumps provide a number of operational benefits for process engineers and plant operators:
- API 610 11th Edition/ISO 13709 full compliance for reliability and accountability
- Suitable with 60 Hz and 50 kW motors
- Near-centerline mounted pump casing maintains alignment during operation at elevated temperatures
- Opposed impeller design for balanced axial thrust for optimal seal and bearing life
- Single suction closed impeller, with large suction eye for low NPSH requirements
- Side-side nozzle arrangement. Nozzles are cast integrally with lower casing half for easy disassembly without disturbing auxiliary pipe work
- Balancing line design for equalizing pressures in seal chambers for optimal seal life
- Highly maintianable and easily replaceable wear rings to reduce overall life cycle costs
- Ring oil lubrication system that incorporates a constant level oiler and sight glass
- Dual volute for balancing radial thrust at each stage and for optimizing seal and bearing life
- Cartridge type mechanical seals for easy assemble and proper installation
- Dynamic flows analysis assures stable performance and high efficiency levels, with high mechanical reliability
- Seal chamber in compliance with API 682 3rd Edition and ISO 21049, ready to accommodate single, tandem or double mechanical seals
- Casings supplied under ASME B16.5 class 600, 900 and 1500
- Cap nuts are arranged on the top half casing parting flange, allowing easy casing removal for rotor inspection and ease of maintenance
- Extra large shaft diameter design to minimize deflection in operation
- Choice of multiple impellers in each hydraulic pump casing for optimum efficiency over a wide operating range
- A variety of instrumentation options are available for monitoring all key operating parameters (temperature, pressure, vibrations and more)
- Socket welded, flanged drains and vents as standard (Gussets and bracing are available)
- Labyrinth bearing seals, deflector, to avoid external contamination and maximizing seal and lubrication life
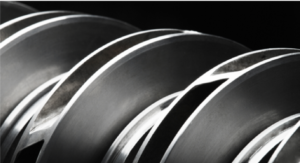
US 60 Hz
- Heads to 4,260 ft
- Flows to 2,640 gpm
- Standards API 610 OH2
- Maximum Motor Power 2500 HP
- Temperature Range -40 to 410°F
- Maximum Case Working Pressure 1,740 psi
- Maximum Suction Pressure 232 psi
- Differential Head 3,937 ft
- Maximum Viscosity Consult Factory
- Mounting Configuration Horizontal-Side-Side
- Seal Configurations API 682
Metric 50 Hz
- Heads to 1,300 m
- Flows to 600 m3/hr
- Standards ISO 13709
- Maximum Motor Power 2,000 kW
- Temperature Range -40 to 210°C
- Maximum Case Working Pressure 120 bar
- Maximum Suction Pressure 16 bar
- Differential Head 1,200 m
- Maximum Viscosity Consult factory
- Mounting Configuration Horizontal-Side-Side
- Seal Configurations API 682
Part | S1 | S5 | S6 | S8 | C6 | A8 | D1 |
Pressure Casing | Carbon Steel (A216 WCB) | 12% CHR | 316 AUS | Duplex | |||
Impeller | Cast Iron | Carbon Steel | 12% CHR | 316 AUS | 12% CHR | 316 AUS | Duplex |
Wear Rings | Cast Iron | 12% CHR Hardened | Hard-faced 316 AUS | 12% CHR Hardened | Hard-faced 316 AUS | Hard-faced Duplex | |
Shaft | Carbon Steel | AISI 4140 | 316 AUS | 12% CHR | 316 AUS | Duplex | |
Bearing Housing | Carbon Steel (A216 WCB) | ||||||
Base Gasket | AUS, Spiral Wound | 316 AUS Spiral Wound | AUS, Spiral Wound | 316 AUS, Spiral Wound | Duplex SS Spiral Wound |