Hydrogen is a chemical element that’s part of naturally occurring compounds, including water and most carbon compounds. Hydrogen has many uses today, mainly in petroleum refining and fertilizer production as ammonia.
Today, as every industry seeks to lower its carbon footprint, the level of interest in using “clean” Hydrogen for power generation, transportation and numerous other applications continues to increase at a rapid pace.
Hydrogen is used as a decarbonization tool because it is a versatile energy carrier, can generate high-heat, and emits no carbon dioxide at the point of combustion. It can be stored for extended periods of time, making it a valuable complement to other renewable sources in the electricity system.
Hydrogen can be produced in different ways, and a color-code naming convention is used to identify the method and carbon intensity of the product:
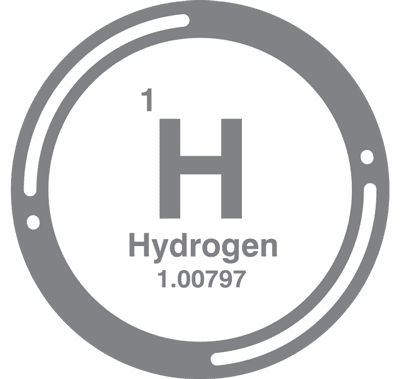
Grey Hydrogen
Produced by steam reforming of natural gas. Today, this is the most common process.
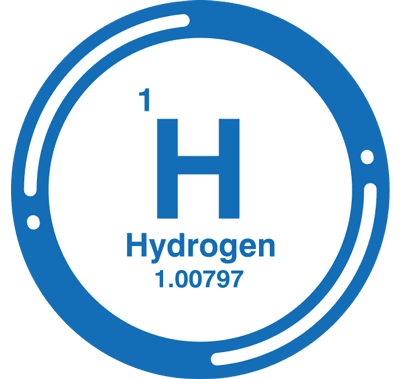
Blue Hydrogen
Produced by steam reforming of natural gas, but the resulting CO2 emissions are captured.
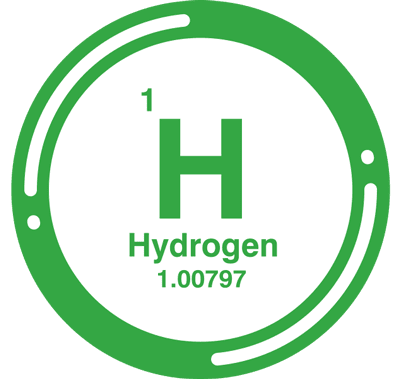
Green Hydrogen
Produced by water electrolysis using only electricity that’s been generated by renewable sources (solar/wind, etc).
Clean hydrogen is one of the most versatile decarbonization solutions available. Sundyne has pumps and compressors to support a wide-range of hydrogen production methods, hydrogen storage and distribution pathways, and hydrogen end-use applications.
To learn more about Sundyne’s value proposition for Clean Hydrogen, click here to view our Clean Hydrogen Value-Chain brochure. We have mapped process flow diagrams covering a range of common processes in Clean Hydrogen markets and identified where our product portfolio offers superior solutions.
Our Hydrogen and Carbon Capture Applications brochure shows how Sundyne’s unique combination of pumps & compressors, support and application expertise offers a total product lifecycle, 360° service for the environmentally safe & leak-free processing of critical gases and liquids. In this brochure, you’ll find our performance characteristics for key equipment in Hydrogen production along with our value proposition in these services.
Industries & Applications:
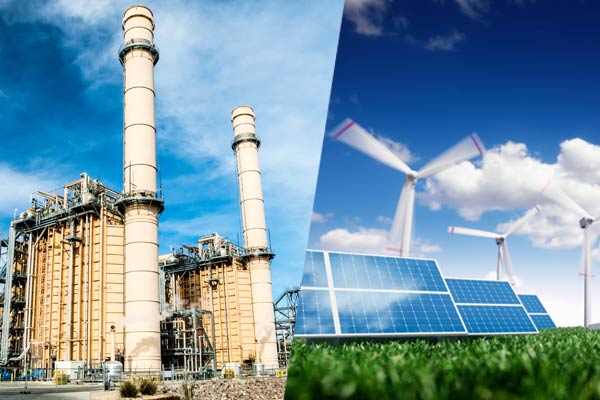
Power Generation
Hydrogen can be stored, which makes it an attractive complement for balancing fluctuating & intermittent sources of renewable energy. In power generation, hydrogen is one of the leading options for storing renewable energy, and hydrogen and ammonia can be used in gas turbines to increase power system flexibility. Ammonia could also be used in coal-fired power plants to reduce emissions.
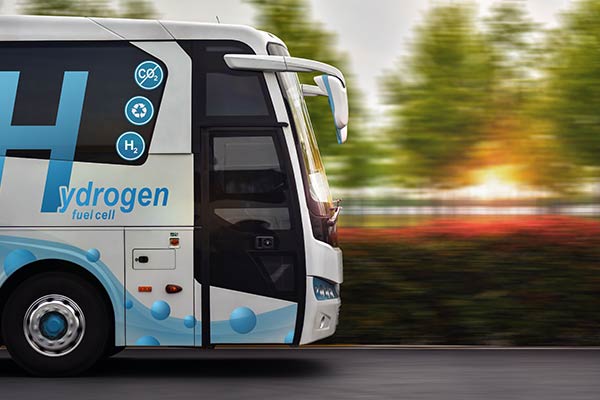
Transportation
Fuel Cell technology makes industrial vehicles & long haul buses emission free. The hydrogen (H2) used in vehicles is an odorless gas that’s normally produced by extracting hydrogen from water or from natural gas. In transport, the competitiveness of hydrogen fuel cell cars depends on fuel cell costs and refuelling stations while for trucks the priority is to reduce the delivered price of hydrogen. Shipping and aviation have limited low-carbon fuel options available and represent an opportunity for hydrogen-based fuels. Click here to learn how Hydrogen Fuel Cells work.
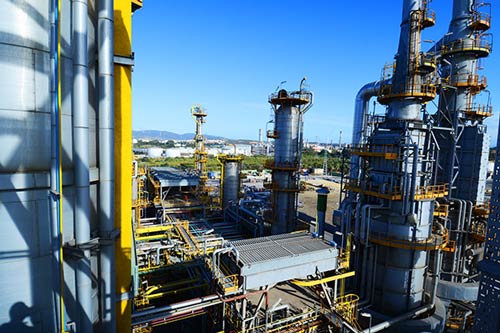
Refineries
Many refineries are investigating how chemically-transformed hydrogen can be used to produce alternative fuels. Hydrogen use today is dominated by industry, namely: oil refining, ammonia production, methanol production and steel production. Virtually all of this hydrogen is supplied using fossil fuels, so there is significant potential for emissions reductions from clean hydrogen.
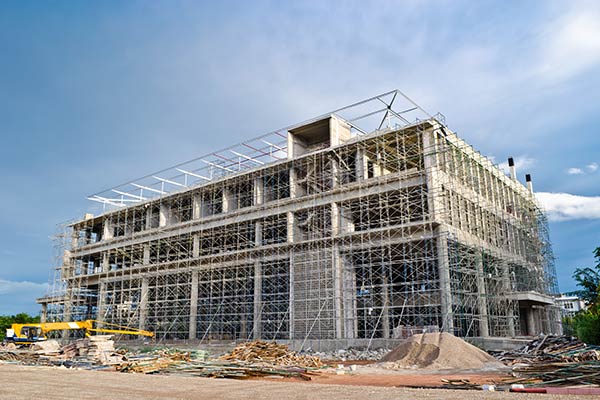
Construction / Industrial
These markets see Hydrogen as a potential alternative to heat commercial buildings. In buildings, hydrogen could be blended into existing natural gas networks, with the highest potential in multifamily and commercial buildings, particularly in dense cities while longer-term prospects could include the direct use of hydrogen in hydrogen boilers or fuel cells.
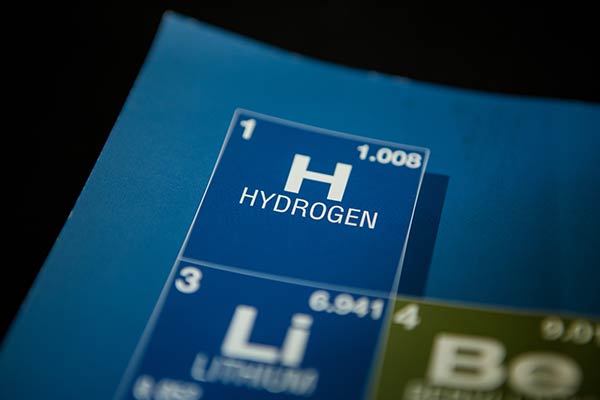
Chemical Industry
Has a long history of processing hydrogen to make hundreds (or thousands) of products that people use every day. Hydrogen is also produced as a byproduct of many chemical processes.
How are Pumps & Compressors used to Process Hydrogen?
For more than 20 years, Sundyne’s compressors and pumps have played an important role in the production, transportation and distribution of Hydrogen around the globe. Sundyne’s PPI compressors are specifically designed to address the challenges associated with compressing H2 from low pressure levels (such as electrolyser outlet pressure) up to the 350 or 700 bar levels that are required by today’s vehicles that run on Hydrogen.
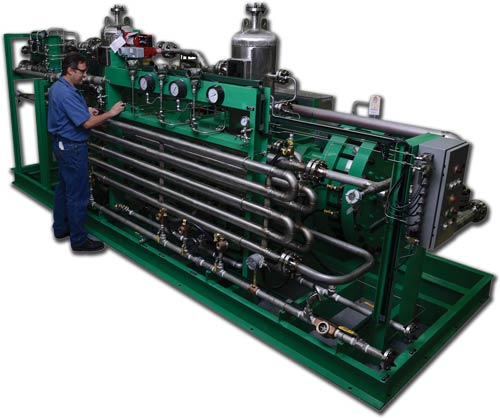
The Centrifugal Integrally-Geared Compressors in the LMC/BMC/LF-2000 series are engineered to optimize the efficiency of hydrogen compression for Energy, Petrochemical, Chemical and Industrial businesses. Available from 100 to 17,000 m3/hr, these compressors are a preferred choice for H2 gas applications.
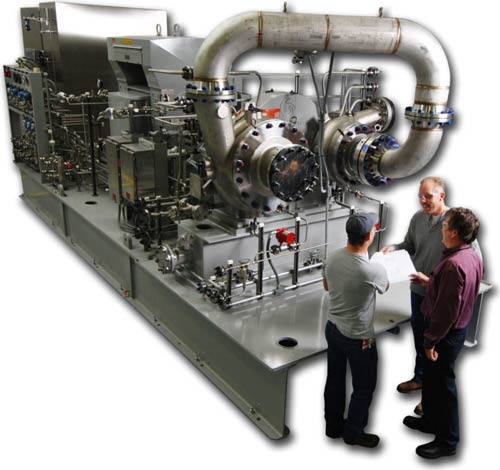
ETFE-lined Ansimag pumps or HMD Kontro metallic pumps offer proven solutions for pumping Potassium Hydroxide (or other chemicals used for pH control) within electrolyser skids. Sundyne’s magnetic drive sealless pumps feature a compact footprint (with no seals or seal support systems), which is critical due to skid space constraints. Sealless pumps also eliminate the danger of emissions or leaks, and they are easier to install, operate and maintain.
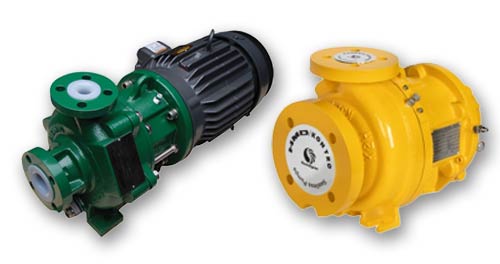
What are the Requirements for Compressors used in Hydrogen Applications?
High Compression Ratio
Diaphragm compressors are designed to meet the pressures required by mobility applications and industrial de-carbonization projects. Multiple members in the Sundyne product family ensure a custom-fit for a wide range of Hydrogen applications.
Product Purity
Diaphragm compressors such as the PPI line feature triple diaphragm sets which ensure that the process gas is isolated from the hydraulic oil. This provides absolute process purity, which is critical for fuel cell applications – as even the slightest contamination can damage the fuel cell.
Environmental Safety
The static seals in compressors must ensure zero leakage of process gas to the atmosphere, and Leak Detection Systems are required to detect any potential diaphragm or seal failure.
Reliability
Every process-contacting part in a Sundyne compressor is made from corrosion resistant alloys, making them ideal for hydrogen processing, as well as other applications involving hazardous gasses.
Lower Energy Costs
Sundyne’s compressors are specially designed to deliver maximum compression at the lowest energy cost.
Explosion-Proof Certification
To assure compliance with global standards for explosion-proof environments.
Support for Industry Standards
PPI Compressors are available in most industry standards.
Custom Engineering
Sundyne collaborates with customers to manufacture customized systems that are optimized for the gas pressure, molecular weight, heat, corrosion, and velocity of each customer’s application. Sundyne utilizes the latest technology in solids modeling and FEA analysis to ensure that all working components are designed & tested to minimize wear, improve sealing and reduce corrosive & erosive effects.
Global Support
Sundyne’s global network of channel partners provide prompt & complete support anywhere around the globe.