We use Sundyne pumps and compressors for specialty services. We require low volume, high pressure pumps and compressors, Sundyne’s integral gear design is unique and fits our process specifications.
Reliable, Compact and Efficient Pumps and Compressors for Downstream Refining
Oil refineries are large industrial facilities loaded with complex piping networks to transport crude oil and its derivatives to different process units for conversion into fuels, oils, distillates and petrochemical feedstocks. Oil is offloaded from ships, railcars, pipelines and trucks into large tanks. Operators heat the oil to crack into hydrocarbons and push them up large distillation columns where they evaporate and are separated. The process is repeated in different areas of the refinery as the derivatives are processed into a variety of products, such as naptha, gasoline, diesel fuel, asphalt, heating oil, kerosene and liquefied petroleum gas. Most refineries have thousands of pumps installed to process and move crude oil and its derivatives. With a broad portfolio of pumps and compressors available, Sundyne offers API / ISO process pumps and compressors for virtually every step of the oil refining process.
Crude Oil Processing
Separating crude oil into different hydrocarbon groups most commonly through distillation.
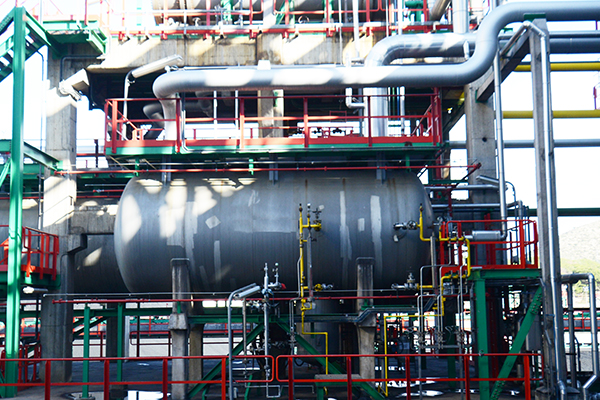
Desalting
Prior to distillation, crude oil is often desalted to remove corrosive salts as well as metals and other suspended solids. Desalting removes calcium, sodium and magnesium chlorides. This keeps deposits from forming and causing plugging later in the refining process.
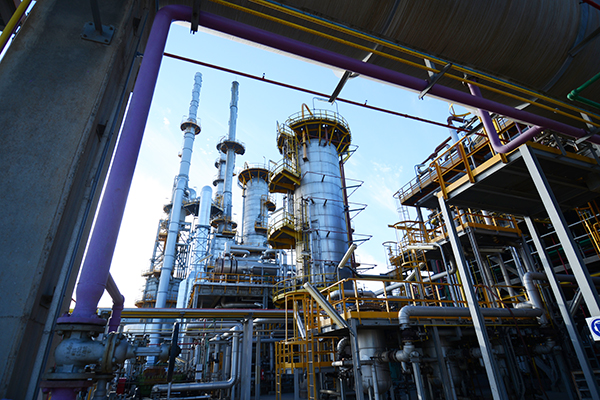
Atmospheric Distillation
Separates desalted crude into specific hydrocarbon groups or fractions. The low boiling fractions of crude oil are separated by atmospheric distillation. Low boiling fractions usually vaporize below 400 °C at atmospheric pressure without cracking the hydrocarbon compounds. . A crude distillation unit (CDU) consists of pre-flash distillation column. The petroleum products obtained from the distillation process are light, medium, and heavy naphtha, kerosene, diesel, and oil residue.
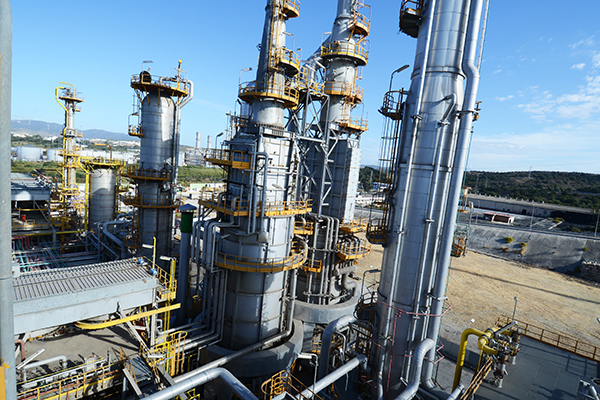
Vacuum Distillation
Heavy crude residue (bottoms) from the atmospheric column is separated using a lower–pressure distillation process. This technique is used when the boiling point of the desired compound is difficult to achieve or will cause the compound to decompose. A reduced pressure decreases the boiling point of compounds. At low pressures, the boiling point of the ADU bottoms is low enough that lighter products can vaporize without cracking or degrading the oil.
Cracking
Cracking or breaking down large, heavy hydrocarbon molecules into smaller hydrocarbon molecules through the application of heat (thermal) or through the use of catalysts.
.
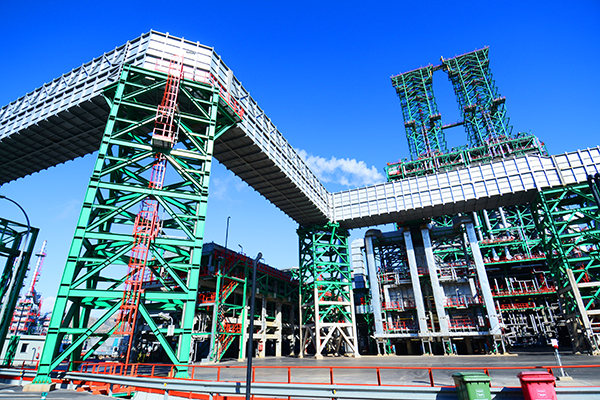
Coking
This thermal, non–catalytic cracking process converts the residual oil from the vacuum distillation column into low molecular-weight hydrocarbon gases, naphtha, light and heavy gas oils, and petroleum coke. The process thermally cracks the long chain hydrocarbon molecules in the residual oil feed into shorter chain molecules leaving behind the excess carbon in the form of petroleum coke.
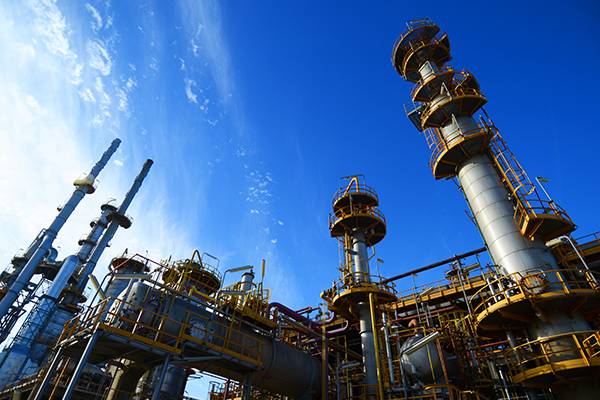
Visbreaking
Thermal non–catalytic process used to convert large hydrocarbon molecules in heavy feedstocks to lighter products such as fuel gas, gasoline, naphtha and gas oil. This process produces middle distillates which reduce the viscosity of the heavy feed. A visbreaker thermally cracks large hydrocarbon molecules in the oil by heating them in a furnace to reduce viscosity and to produce small quantities of light hydrocarbons (LPG and gasoline). The name visbreaker refers to the fact that the process reduces or breaks the viscosity of the residual oil.
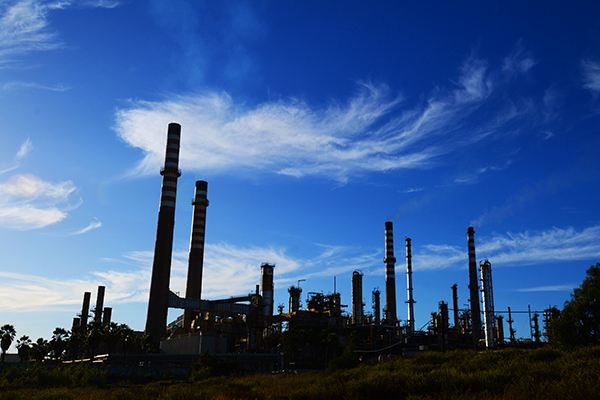
Catalytic Cracking
Heavy oil is passed through metal chambers (called catalytic crackers or cat crackers) under pressure and high temperature in the presence of catalysts such as alumina, silica or zeolites. This boiling breaks up heavy, large and more complex long-chain oil molecules into lighter, smaller and simpler short-chain molecules, such as those of gasoline, olefinic gases and other products.
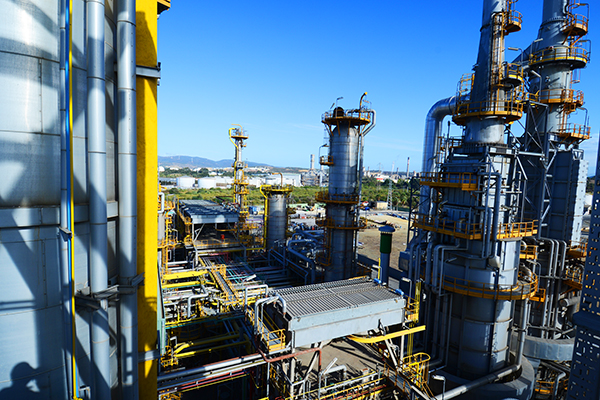
Catalytic Hydrocracking
Like cracking is used to produce blending stocks for gasoline and other fuels from heavy feedstocks. It converts linear molecules to higher octane branched molecules for blending into gasoline or feed to alkylation units. Introduction of hydrogen (in addition to a catalyst) allows the cracking reaction to proceed at lower temperatures than in catalytic cracking, although pressures are much higher
Combination
Linking two or more hydrocarbon molecules together to form a large molecule (e.g. converting gases to liquids) or rearranging to improve the quality of the molecule.
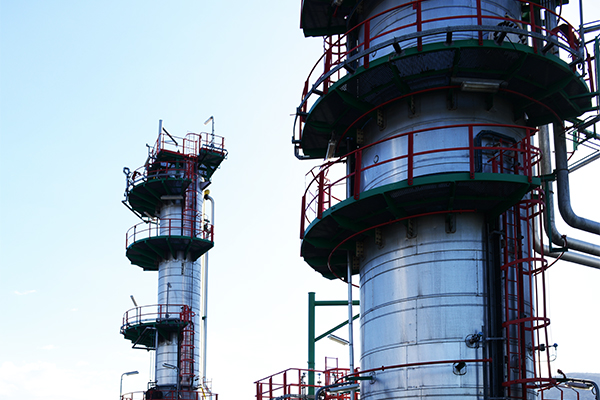
Alkylation
Is the process of upgrading light olefins to high–value gasoline components. It is used to combine small molecules into large molecules to produce a higher octane product for blending with gasoline.
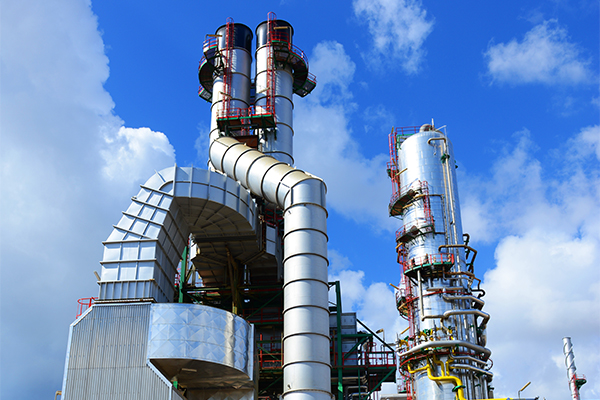
Catalytic Reforming
The process whereby naphthas are changed chemically to increase their octane numbers. Octane numbers measure whether a gasoline will knock in an engine: the higher the octane number, the more resistance to pre-ignition or self-ignition.
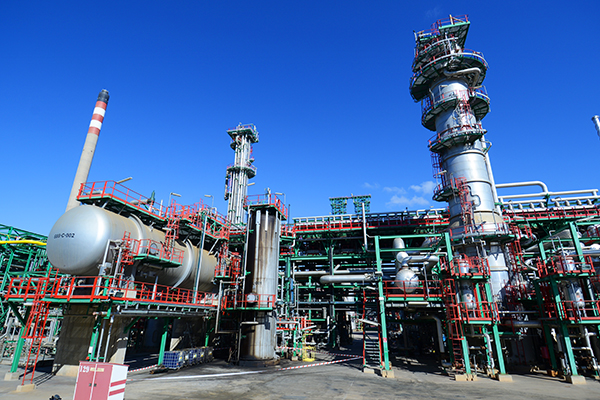
Polymerization
The controlled process by which olefin gases are converted to liquid condensation products that are suitable for blending stock in gasoline or other liquid fuels. The feedstock usually consists of propylene, propene and butylenes (butenes) from cracking processes.
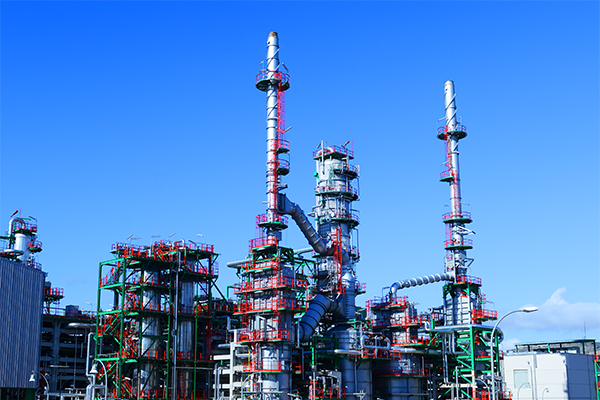
Isomerization
Is the process used to produce compounds with high octane for blending into the gasoline pool. It is also used to produce isobutene, which is an important feedstock for alkylation.
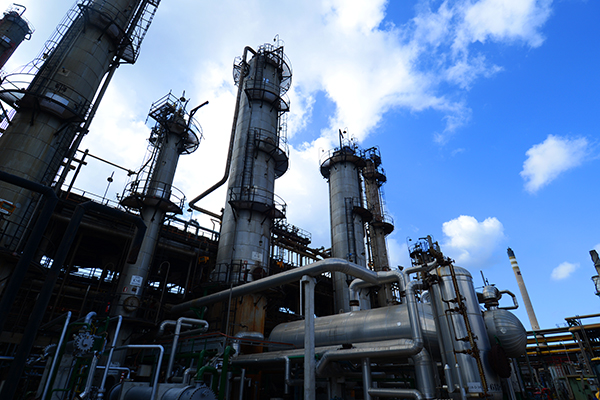
Hydrotreating
Is used to remove impurities (e.g. sulfur, nitrogen, oxygen and halides) from petroleum fractions. Hydrotreating further upgrades heavy feeds by converting olefins and diolefins to parafins, which reduces gum formation in fuels.
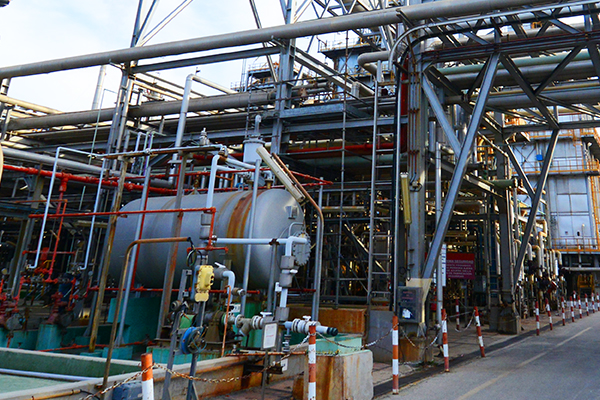
Sour Water
Wastewater is produced from atmospheric and vacuum crude columns at refineries. Hydrogen sulfide and ammonia are typical components in sour water that need to be removed, before the water can be reused elsewhere in the plant. Removal of these components is done by sending the sour water from the process to a stripping tower where heat, in the form of steam, is applied. The ammonia and hydrogen sulfide contained in the water is released by the heat and exits the top of the tower. Sundyne pumps are specifically suited to handling wastewater at the high pressures required to send liquids through a stripping tower.