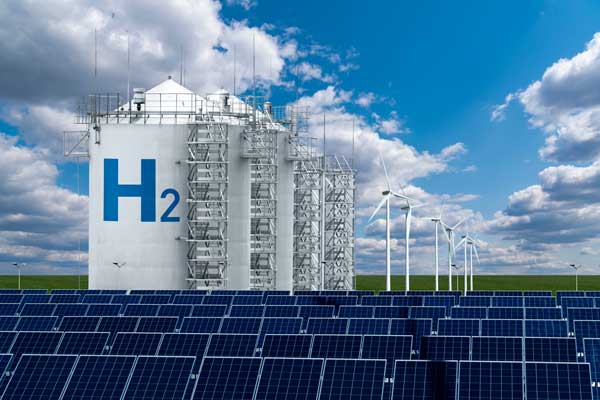
What is the Clean Hydrogen Value Chain?
Clean Hydrogen refers to hydrogen that is produced in a manner that minimizes or completely eliminates greenhouse gas emissions. The two main pathways for clean hydrogen production are:
- Green Hydrogen: produced by electrolysis of water powered by renewable electricity.
- Blue Hydrogen: produced by reforming natural gas with carbon capture installed to capture the CO2 emissions generated in the process.
The Clean Hydrogen Value Chain consists of all processes used in the production, distribution (including hydrogen storage), and end-use of clean hydrogen.
What are the current and emerging uses of clean hydrogen?
Historically, the main uses of hydrogen are ammonia production for fertilizers and in petroleum refining. As of 2024, approximately 95% of global hydrogen production was “gray” hydrogen – meaning it was produced from natural gas or coal without carbon capture.
In the Energy Transition, clean hydrogen has become an important decarbonization solution because of its versatility and characteristics as an energy-carrier. Emerging applications for clean hydrogen include fuel-cell electric vehicles, synthetic fuel production, blending with natural gas for industrial heat or power generation, and displacing all “gray” hydrogen uses with a clean alternative.
How is clean hydrogen distributed and stored?
Once produced, clean hydrogen can be transported to an end-use location or stored until needed. One of the benefits of hydrogen is that it is an energy carrier and can be produced when and where it is economical, and then utilized when and where it is needed.
Hydrogen can be transported as a gas, liquid, or converted to liquid ammonia. As a gas, hydrogen can be transported in pipelines or tube trailers. For longer distance transportation at higher volumes, hydrogen is often converted to ammonia to increase its energy density. Then, at the receiving end, the ammonia can be converted back into hydrogen via ammonia cracking for any end-use.
For storage, hydrogen can be pressurized and stored as a gas or a liquid. For small-scale applications, hydrogen is often stored onsite in composite tanks. For larger-scale applications and long-term storage, hydrogen can be stored underground in salt caverns.
What pumps and compressors are used in clean hydrogen?
Sundyne offers a range of pumps and compressors used in Clean Hydrogen production, transportation, storage, and end-use.
Key applications of Sundyne’s portfolio include sealless pumps on electrolyzers for circulation, diaphragm compressors for leak-free H2 compression, and centrifugal compressors for recycle gas, regeneration, and H2-drying services. Sundyne has global experience providing rotating equipment for critical hydrogen services.
Sundyne is working with electrolyzer OEMs, leading EPCs, and end-users across the value-chain to design and manufacture high quality rotating equipment. Please reach out to our team if you have any hydrogen applications and would like to learn more!
Why are sealless pumps a good choice for electrolyzers?
Electrolyzers are the critical technology component used in green hydrogen production. Electrolyzers use electricity to split water into hydrogen and oxygen through a process called electrolysis. Electrolyzers are often built as modules which are stacked together in a plant. Each electrolyzer module typically has sealless pumps dedicated to circulate water or the electrolyte fluid.
Sundyne’s sealless pumps offer a compact footprint, high reliability and simple maintenance since they do not have seals or seal support systems. Sealless pumps also handle caustic chemicals well and provide total fluid containment, which eliminates the risk of leaks.
See our past post on sealless pumps for electrolyzers for more information!
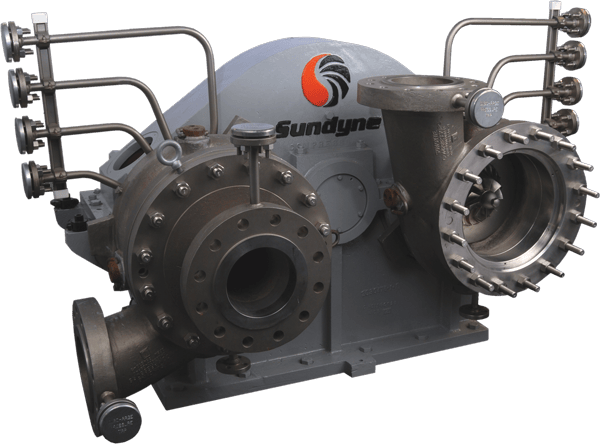
Sundyne LMC / BMC / LF-2000 Compressors
Sundyne compressors leverage more than 60 years of experience and innovation from thousands of deployments in some of the world’s most demanding environments. Sundyne compressors feature single- and multi-stage integrally-geared centrifugal designs (IGC) that are custom built to provide pulsation- and vibration-free operation, and to deliver oil-free process gas with zero emissions.
Sundyne IGC compressors offer a unique combination of high-performance impeller materials and advanced geometry, optimized for high-speed operation, delivering exceptional compression ratios for hydrogen applications. With hundreds of compressors already in use for H2 purification and boosting processes, our technology is proven and reliable.
Additionally, Sundyne compressors, utilized as fuel gas boosters for turbines generating electricity, are fully capable of handling hydrogen-natural gas blends. Existing installations can be easily retrofitted to meet new performance requirements, supporting CO2 reduction initiatives.
PPI Compressors
Sundyne enables organizations to deliver Net-Zero through sustainable, safe and environmentally conscious compression solutions with the broad portfolio of advanced Hydrogen compressors and packages renowned for highly reliable, leak-free performance that deliver the critical non-contaminating compression of Hydrogen. This makes PPI the ideal compressor for Hydrogen production, storage and distribution. Aftermarket support for PPI Diaphragm compressors is provided via Sundyne’s global network of channel partners.
Sundyne LMV and HMP Pumps
Sundyne integrally geared centrifugal pumps are optimized for low flow-high head applications. They offer the highest efficiency in the low flow range with a proven track record of high reliability. A single impeller in a Sundyne LMV pump spins at high speed to produce the same head as a multistage pump running at synchronous speed. Sundyne LMV pumps are ideally suited for services such as boiler feed water pumps, condensate transfer pumps, solvent circulation pumps and reflux pumps. To achieve higher heads yet, two or more integrally geared stages run in series in a Sundyne HMP pump. The compact design reduces installation costs, and the simplicity limits the number of spare parts while making maintenance easier.
Marelli Pumps
Marelli pumps leverage a track record of more than 60 years in centrifugal pump design, development, manufacturing and service. Marelli caters to global markets from conventional oil & gas and petrochemicals to fast evolving Clean Energy segments, including green/blue hydrogen, ammonia, carbon capture, and renewable fuels processing. Marelli covers API-610 in OH, BB and VS types and meets a wide range of stringent customer specifications.
Sealless Magnetic Drive Pumps – HMD and ANSIMAG
Sundyne sealless pumps provide optimum safety and environmental protection for a wide range of applications found within Hydrogen Electrolysis, Ammonia Synthesis and E-methanol production. These magnetic driven pumps are designed for harsh and hazardous liquids, and applications that are difficult to seal. HMD Kontro metallic and Ansimag ETFE-lined sealless pumps ensure total product containment, increased reliability & uptime and simplified maintenance with no seals or seal support systems, whilst meeting industry standards such as ASME, ISO and API.
Sundyne sealless pumps are particularly well suited to alkaline and PEM circulation applications in H2 electrolysis due to their compact footprint and simple, easy-to-maintain design. The seal-free design eliminates the risk of emissions of harmful product such as KOH or contamination of the pumped medium which is critical for high purity applications found in PEM Electrolyzers. The HMD ZeroLoss shell provides a high energy efficiency solution for a wide range of services including Methanol, Ammonia and Solvents. Options for Secondary Control and Containment are available to provide additional protection for more hazardous pumping applications.
Sunflo Pumps
Industrial grade Sunflo pumps are specifically designed for low flow high head applications such as boiler feed water, condensate and demineralized water circulation. Sunflo pumps leverage the engineering knowledge and legacy of the Sundyne heavy duty API integrally geared pumps. A single impeller runs at high speed to produce high heads in a very compact and reliable design. The close coupled configuration eliminates alignment, simplifies installation while further reducing footprint. The Sunflo cartridge shaft assembly comes complete with all the rotating parts and enables quick and easy servicing of the pump in-place.
How can I learn more?For additional examples and to see an overview of where our rotating equipment portfolio fits into Clean Hydrogen processes, refer to our market brochure. If you would like someone from Sundyne to contact you, please click here. |
![]() |