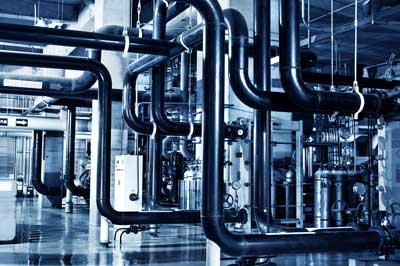
Boilers heat water to make steam. Steam is used to heat buildings (via radiators) and it’s also used to make power via steam turbines. High pressure steam performs the mechanical work that turns steam turbines. Every power plant (from large utilities to smaller co-gen plants in universities, hospitals or industrial buildings) has an optimal steam velocity for its process. Water can flow through piping at velocities of 15 to 25 feet/second – but steam line velocities can range as high as 400 feet/second. The boiler feed pump is the heart of the process, because it keeps water flowing into the boiler, to ensure that steam can be generated in an uninterrupted fashion.
Which Types of Pumps are used to Feed Boilers?

Centrifugal pumps are the preferred choice for boiler feed applications.
High flow is a primary requirement, because boilers require continuous feed water.
- Co-generation power plants typically require pumps with flows up to 500 GPM (125 m3/hr), with heads up to 3,000 feet.
- Larger utility-scale power plants often use heavy-duty BB3 multi-stage pumps that can deliver flows up to 2,640 gpm (600m³/hr). Some utilities prefer horizontal axial split case pumps, running back-to-back impellers in heavy-duty double volute casings for boiler feed applications.
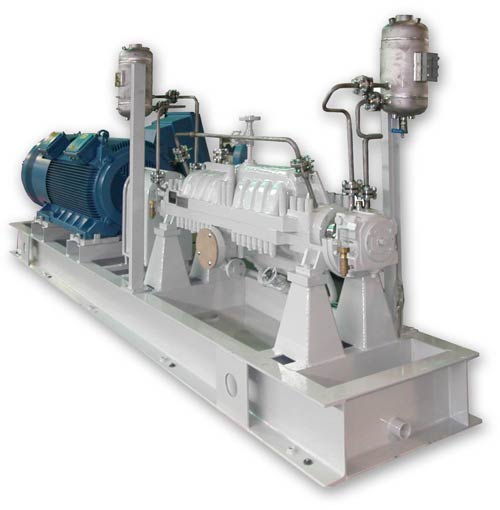
High Temperature & High Pressure are also key requirements. Boiler feed pumps must be capable of generating enough pressure to overcome the steam pressure in the boiler. Water changes to gas at 212°F, but boiler feed water can range anywhere from 225°F up to 350°F. In order to maintain feed water in a liquid state, the pump (and the inlet piping) must maintain pressures that are higher than the water vapor pressure.
- Co-gen plants typically require pumps that can deliver heads up to 3,000 feet, with temperature ranges that can exceed 410°F (210°C).
- Larger Utilities may opt for pumps that can deliver heads to 4,260 feet (1,300 m), with similar temperature ranges, up to 410°F (210°C).
Condensate Pumps:
Once steam passes through and exits the turbine, it is routed to cooling towers and condensers, which turn the steam back into warm water. Often times, impurities (such as carbonic acid) form at this stage of the process. These impurities can reduce the water’s pH and they could potentially corrode pipes and pumps. As a result, pumps deployed as condensate pumps should be made of stainless steel (or other resistant alloys) so that they can stand up to the rigors of a continuous process.
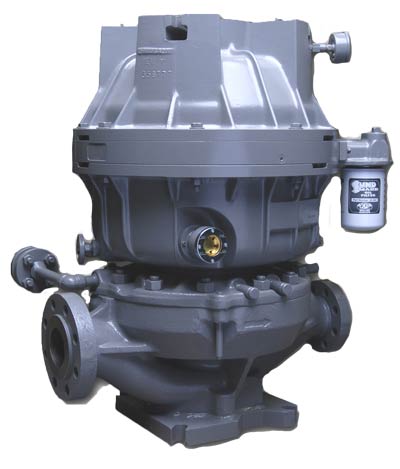
Sundyne integrally geared pumps are widely used to move condensate throughout power generation heat exchanging systems. They provide the ability to safely & efficiently handle high pressure, in a space saving design, with very low maintenance requirements. These features are essential for pumps deployed as condensate pumps.
Each of the centrifugal pumps highlighted in this post plays an important role in improving boiler efficiency, as well as enhancing the overall efficiency of a power plant. For more information, please click here.