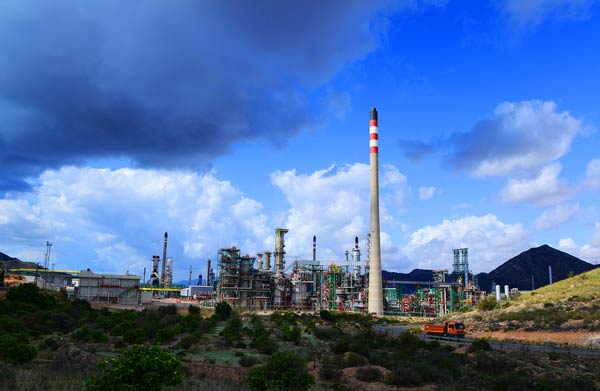
This article identifies areas where Sunflo industrial grade pumps can be deployed, and it also highlights the benefits of using a Sunflo pump in specific areas versus an API-610 pump.
What are the different types of pumps and their industrial applications?
Pumps move liquid (while compressors move gas). Pumps play a critical role in industrial applications, such as manufacturing, food & beverage processing, mining, chemical processing, power generation, and in the energy industries such as oil & gas production and refining.
What are the most common process pump types?
The most common types of process pumps are typically API 610 pumps, which include:
- OH (Overhung) pumps: OH1 and OH2 designations are horizontal pumps. OH3-OH6 designations are Vertical In-line pumps.
- BB (Between Bearings) pumps: BB1 pumps are 1&2 stage pumps that are Axially Split. BB2 pumps are also 1&2 stage pumps, but are Radially Split. BB3-BB5 pumps are multi-stage pumps that can feature single or double casings.
- VS (Vertical Suspended) pumps: different suffix numbers denote the following: VS1 (Diffuser), VS2 (Volute), VS3 (Axial Flow), VS4 (Line Shaft), VS5 (Cantilever), VS6 (Diffuser, Double Casing), and VS7 (Volute, Double Casing).
Which type of pumps are used in the hydrocarbon processing industries?
Often times, pumps deployed in hydrocarbon processing industries are API pumps. The American Petroleum Institute (API) defines the standards for ultra-reliable process pumps. API 610 was born out of the needs of refineries, to address the demands that come with handling high-temperature hydrocarbons with extreme reliability and safety requirements. In addition to refineries, this standard applies to other industries that require mission-critical pumping. Some facility operators and engineering firms use API 610 as a starting point and add their own plant-specific overlays. The API spec can be tailored to a variety of applications.
Pumps adhering to API standards are more expensive than other pumps. This is due to stipulations that mandate supreme quality (and redundancy in some cases) when it comes to items such as: casing and casing connections, mechanical shaft seals, seal support systems, bearing housing oil-level management systems, baseplates, documentation and other stipulations. Adhering to API standards results in a high quality, highly reliable pump – but in many cases the operator ends up with “more pump than is necessary” to accomplish the task. Every pump application presents its own unique set of conditions, so the “off-the-shelf” API spec is not always appropriate (in its entirety), and full adherence to the standard often times results in a pump that is “over spec’d” for the application.
How do operators address the needs for highly reliable, high pressure pumps, without having to pay for all the “bells & whistles” that come with an API pump? The answer is industrial grade pumps – such as Sunflo Pumps.
Single stage Sunflo pumps leverage the engineering knowledge and legacy of the Sundyne heavy duty API integrally geared pumps to create industrial grade pumps that save energy and water through efficient high-pressure pumping. Industrial grade Sunflo pumps are specifically designed for High Pressure applications, such as boiler feed, NOx suppression, reverse osmosis or high pressure wash down applications that are common to power generation, maritime, transportation or food & beverage industries.
Sunflo Industrial-Grade high-pressure pumps feature thrust bearings as part of their unique modular shaft assembly, which are sized to handle axial thrust without problematic balancing devices. The impellers on Sunflo pumps feature unique suction inducer technology, which is optimized to deliver low NPSH requirements – eliminating pump cavitation. Sunflo pumps also leverage Sundyne’s field-proven high pressure impeller technology that is optimized to deliver high head.
Sunflo pumps are well suited to address the aggressive nature of boiler feed water applications, featuring 316-stainless steel construction as a standard, with higher alloys available, compared to segmented ring pumps that are commonly constructed from cast iron or carbon steel. The single-stage design simplicity and compact footprint requires approximately 50-percent less steel than segmented ring pumps.
Sunflo pumps feature an efficient seal cooling process, which recirculates the process fluid from the seal chamber through a seal flush cooler and back into the seal chamber. This efficient process reduces fouling and requires less water and energy for cooling, compared to API-Plan 21 cooling processes, which are widely used with segmented ring pumps.
All of these features enable Sunflo Industrial Grade pumps to withstand upset conditions that are common to cogeneration power plants. In addition to boiler feed applications, Sunflo Industrial Grade pumps are also used in power plants for applications such as: NOx suppression, equipment wash-down, surface cleaning and tank cleaning.
In addition to power generation applications, Sunflo industrial grade pumps are widely used in upstream oil & gas applications, for utilities (such as water for the staff on the platform), and for high pressure wash-down and cleaning applications.
In the Food & beverage industry, Sunflo pumps serve a wide variety of applications, such as:
- High pressure wash-down, deboning/descaling…
- Tank cleaning & central cleaning systems
- Poultry and livestock processing
- Crab cleaning
- Fish scale removal
- Odor control
- Dust suppression
To learn more, please click here.