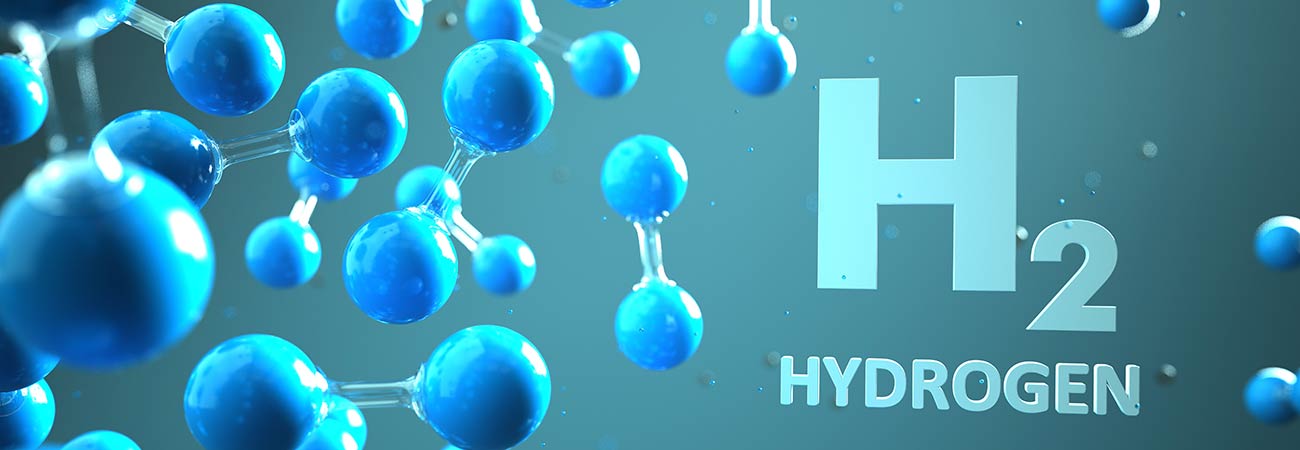
Hydrogen is a versatile energy carrier. It is one of the most efficient fuels on Earth, with the highest energy content per weight. Hydrogen can be stored for extended periods of time, making it a valuable complement to other renewable sources in the electricity system.
Hydrogen can be produced from almost all energy resources. A color code system identifies the different means:
- Grey Hydrogen – is produced by steam reforming of natural gas. Today, this is the most common process.
- Blue Hydrogen – comes from the same process, but the resulting CO2emissions are captured and stored (CCS).
- Green Hydrogen – is produced by water electrolysis using only electricity that’s been generated by renewable sources (solar/wind, etc).
Di-hydrogen is one of the smallest molecules on the planet, weighing no more than 2.02 grams per mole (whereas ambient air is close to 29 g/mole). In order to attain functional levels of energy density, hydrogen compressors are required.
Unlike liquids, which are relatively incompressible, gases (like Hydrogen) are compressible. Compression is achieved by moving Hydrogen through a compressor that decreases the gas’ volume between the inlet and discharge (some compressors feature more than one stage of compression). Decreasing volume increases the gas’ static pressure. This makes it possible to transport Hydrogen so that it can be stored in tanks. It also boosts the gas’ pressure up to levels that are required by a given process.
As an example, electrolysers typically make Hydrogen at 20 to 30 bar. But many industrial H2-powered vehicles are rated for 350 to 500 bar. Hydrogen compressors, such as Sundyne’s PPI line, are used to compress Hydrogen to make up this difference.
The preferred design for Hydrogen applications is a diaphragm compressor. There are several reasons for this, including:
- Product Purity: the Diaphragm acts as a secure border between the process gas (hydrogen) and the compressor’s hydraulic fluids. PPI compressors feature triple diaphragm sets, which ensure absolute process purity. This is critical for fuel cell applications – as even the slightest contamination can damage a fuel cell.
- High Compression Ratio: PPI compressors achieve compression ratios of 10:1 per stage through careful control of the contoured cavities and clearance volumes. PPI’s 2 stage units use a 180 degree piston offset between each stage of compression – when one head is on the discharge stroke, the second head is on the suction stroke. This results in the highest possible efficiency and lowest power consumption.
- Environmental Safety: The static seals in PPI compressors ensure zero leakage of process gas to the atmosphere, and PPI’s Leak Detection System immediately detects diaphragm or seal failure. PPI compressors are based on the API 618 standard, with some differences due to the diaphragm compressors’ unique design. They also meet all of the various requirements for explosion-proof environments, around the globe.
- Custom Engineering: Sundyne’s Hydrogen compressors are manufactured to specific customer requirements. Each Hydrogen compressor is optimized for the gas pressure, molecular weight, heat, corrosion and velocity of a customer’s application. Sundyne utilizes the latest technology in solids modeling and FEA analysis to ensure that all working components are designed & tested to minimize wear, improve sealing and reduce corrosive & erosive effects.
- Longer Mean Time between Maintenance Intervals: The replacement part life for compressor components is directly related to operational speed. PPI units typically operate in the range of 300-325 rpm. Other manufacturers’ compressors run at much faster speeds, which requires maintenance more frequently, and often results in down time.
For more than 20 years, Sundyne’s compressors have played an important role in the production, transportation and distribution of Hydrogen around the globe. To learn more, please click here.